I have been creating bone china flowers since May 2004 when I volunteered at the Coalport China Museum. At the time, I was in my final years at university and seeking work experience. On my first day, a lovely lady named Mary, who had been a demonstrator at the museum for about 16 years, taught me how to make roses from fine bone china clay. On my third day of practice, three visitors asked me how many years I had been making these flowers. Their astonishment made me giggle as I replied, “Two days!” It seemed my apprenticeship in china rose making was complete, though mastering other flowers like the daffodil, daisy, and carnation took a bit longer. Nevertheless, I felt like a natural. Even before trying, I knew I could make them, having seen similar work at the Gladstone Museum while at university.
This volunteer role led to a job offer when Mary decided to retire. I accepted a job share, working one day a week for a couple of years. Since then, I have continued to stay involved because I love the job so much.
I still enjoy demonstrating and look forward to my odd shifts at the museum. I find it therapeutic and rewarding. My passion for flower making eventually inspired me to develop my flower people.
My Bone China Flowers made at Coalport China Museum
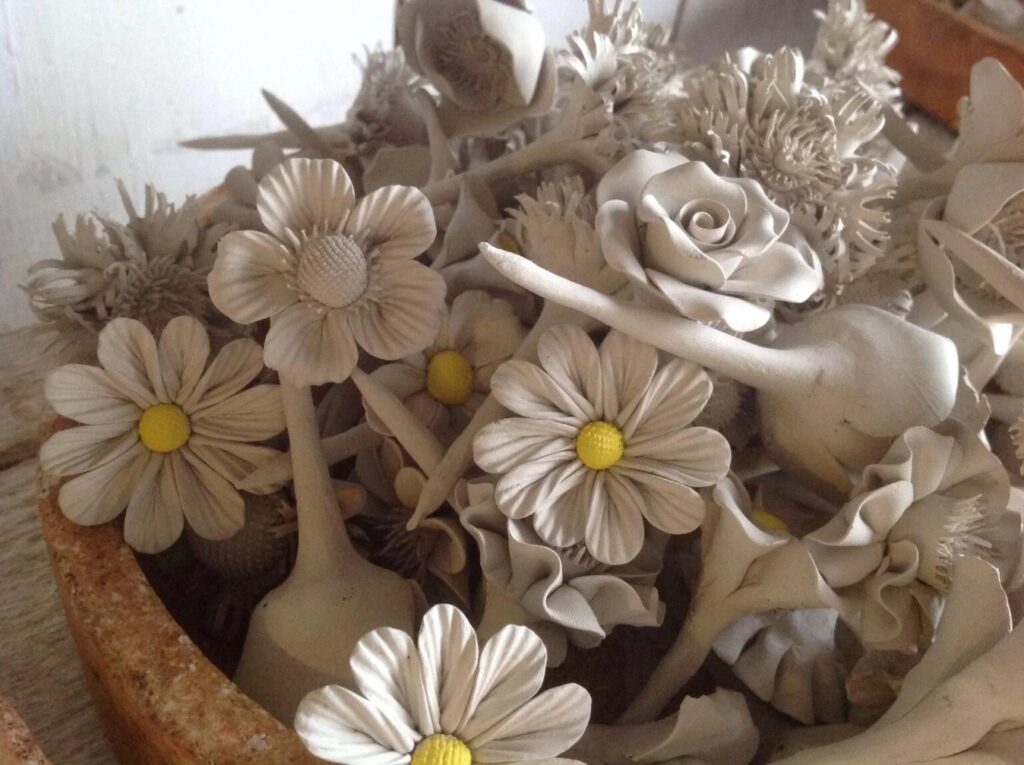
Bone China Clay
Bone china clay is a type of porcelain composed of 50% animal bone ash, 25% china clay (kaolin), and 25% china stone (feldspar). This composition gives it a translucent quality due to the animal bone content, making it the whitest and finest porcelain available. The addition of bone ash also enhances its strength. First developed by Spode in 1799, bone china was soon adopted by all the potteries in England despite its high production costs, as it was finer and whiter than other types of porcelain at the time. This recipe is what makes it English Bone China flowers, gum arabic must be added to the clay. Gum arabic, a plant sap, makes the clay more pliable and is used exclusively for bone china flower-making clay, not in slip. Without gum arabic, creating flowers from bone china clay would be impossible.
Since bone china clay is sticky, oil needs to be applied to the hands to make it more workable.
History of English Bone China Flower Making
Bone china flowers have been hand-made to decorate pottery since the mid-eighteenth century. They were especially popular during the Victorian era when tiny handmade flowers were crafted into brooches and used to adorn bowls and vases.
In the 1800s, Coalport China introduced a range of flower-encrusted pottery known as Coalbrookdale. This line was highly desirable, renowned for its hand-painted and sculpted china featuring intricate ornamentation and vibrant colors.
Bone china flowers were traditionally made by girls who underwent an apprenticeship. Those who showed potential were selected to stay and learn to make a variety of flowers, including roses, daffodils, daisies, and pansies. Each flower was meticulously handmade using simple tools like a comb, which was used to create spiky effects and the centers of daisies. Over time, tools such as tea sieves or metal meshes were also employed.
The girls were paid on a piecework basis, meaning their earnings depended on the number of flowers they made. Aiming to produce around 500 flowers a day, they could earn a decent pay packet for their efforts.
Decoration on Coalport Bone China Flowers
This aspect has always impressed me. When Coalport and other potteries created these elaborate wares, there were numerous opportunities for things to go wrong during the many processes and stages.
Once a piece was made, it underwent a biscuit firing, which took several days. If it survived, it was dipped in glaze and fired a second time. Each color then had to be applied and fired separately, as each color required a different firing temperature. For example, if an object had six colors, it would have been fired eight times. That’s a lot of firings just to achieve a few colors on a plate!
In the past, firing using bottle kilns was a major task. The process took days, and the man in charge, known as the fireman, was the highest paid. Armed with just a shovel and tons of coal (about 15 tons per firing), he had the skill to maintain the kiln at the correct firing temperature without exceeding it. Overfiring would have meant that every other person involved in the pottery-making process would not be paid. The success of the potteries relied heavily on brilliant teamwork.
Today, firings are much simpler. I use a modern electric kiln with a controllable panel where I set the desired temperature and can then leave it to run on its own while I go out shopping. It’s that simple.
The decoration of pottery has also evolved significantly. Nowadays, all colors can be fired together at the same temperature, and color can be added to wet or leather-hard clay and biscuit ware. You can even print a photograph from a laser printer to create your own ceramic transfers.
The Story of Bone China Flower Making – Coalport China Museum

Factories in England using hand-made flowers in their designs included Chelsea, Bow Derby and Minton. ‘Coalbrookdale’ is used as a general term for intricate flower encrusted pottery pieces produced at Coalport.
Handmade porcelain flowers were produced at Meissen in Germany from the early eighteenth century. in 1748 individual flowers accounted for five sixes of the production at the Serves Factory. They were either mounted on wire stems or applied directly to the surface of vases. In the 1750’s the Vincennes factory employed 46 girls making porcelain flowers to be mounted on wire stems with metal leaves.
Madame de Pompadour even had a porcelain flower garden made for wintertime.
Bone china flowers are a well known form of decoration on Coalport China. They were used to decorate a range of Coalport china called Coalbrookdale Ware.
The flowers were made completely by hand from bone china clay.
At the Coalport China Works, this skilled task was usually performed by women. They could each make a china rose in about thirty seconds.
The flower makers required only simple tools.
They would use a comb made from leather, wood or bone to make indentations in the clay and a scalpel for cutting.
The most skilled flower makers had a comb made of bone as a sign of their higher status.
Flower makers today use every day objects such as tea strainers as tools. They rub cooking oil into their hands to prevent the clay sticking.
Bone china clay used to ‘go off’ very quickly and was extremely smelly.
Modern bone china clay contains special chemicals to prevent it ‘going off’ so quickly.