How to make a flower from Clay
Ceramic flower making takes a bit of time and practice. I developed the skill at Coalport China Museum using ancient techniques of bone china flower making. Bone china is a very sticky clay so you use oil such as sunflower oil on your fingers to stop it sticking. It is very soft and can only be sculpted into tiny or palm of the hand size flowers. This is only great for small ceramic clay flowers.
You can make flowers out of any clay with a some of practice. I believe I could teach anyone to make clay flowers. Below are some ‘how to’ guides and videos showing you how to make ceramic flowers using clay. The techniques will work with any clay so can be tried using the air drying clay or other clays you may wish to work with.
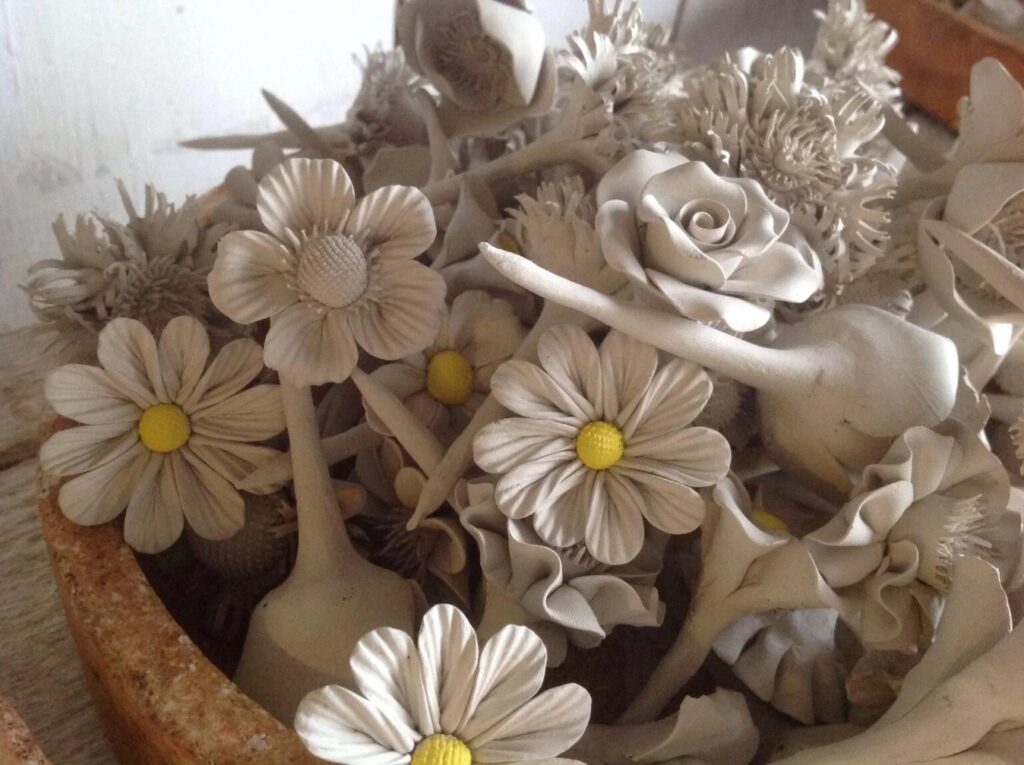
How to make a Poppy out of Clay
Head over to the page below to learn how I Poppies out of clay. Any clay will work as long as its soft and wet enough.
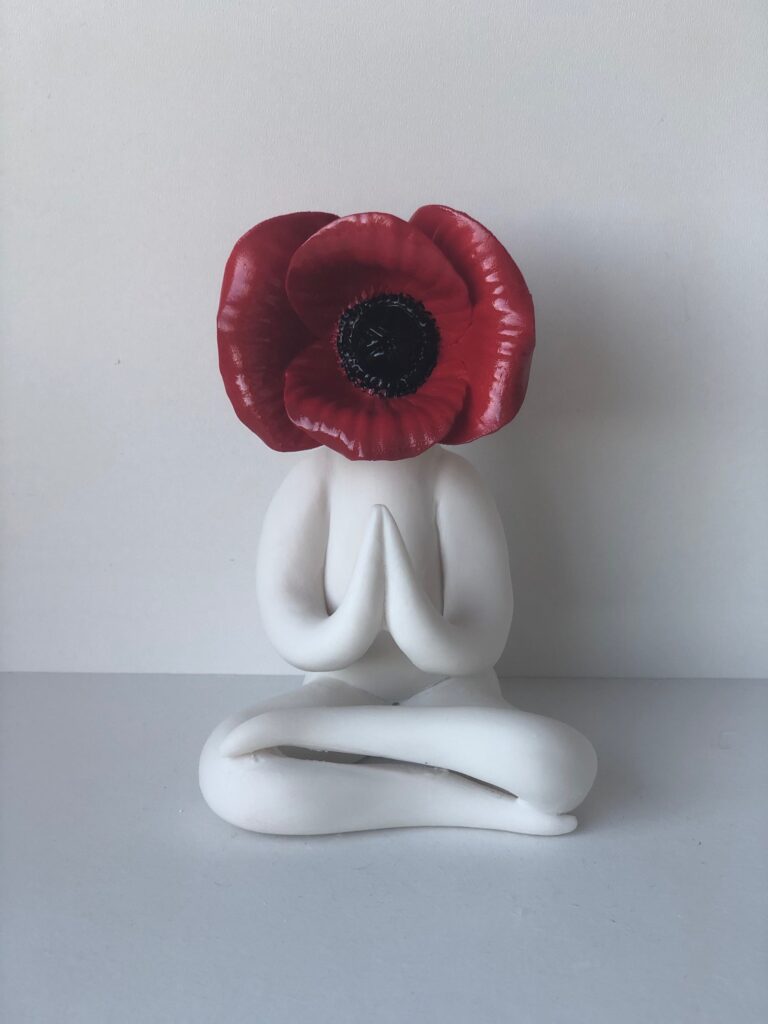
How to make a Daffodil out of Clay

How to make a Tuberose out of clay

Bone China Flower Making
Making a Rose Flower using Bone China Clay
Making a Poppy Flower using Bone China Clay
Making a Daffodil Flower using Bone China Clay
History of Ceramic Flower Making
Bone china flowers have been hand-crafted to adorn pottery since the mid-eighteenth century. They were especially popular during the Victorian era, where these delicate flowers were fashioned into brooches and added as decorations to bowls and vases.
In the 1800s, Coalport China introduced a range of flower-encrusted pottery known as Coalbrookdale ware. This collection was highly coveted for its intricate hand-painted and sculpted details, renowned for its ornate designs and vibrant use of color.
The art of making bone china flowers was a skill reserved for girls who had completed an apprenticeship. Those who demonstrated exceptional talent were selected to continue and trained to create a variety of flowers, including roses, daffodils, daisies, and pansies. Each flower was meticulously crafted by hand using simple tools like a comb, which was employed to create spiky textures and the center of a daisy. Over time, other tools such as tea sieves or metal meshes were also utilized.
The girls were paid based on piecework, meaning their earnings depended on the number of flowers they produced. A target of 500 flowers a day was common to ensure a decent wage.
Decoration on Coalport Bone China
The elaborate decoration of Coalport and other potteries always fascinated me. There were numerous stages where things could go wrong during production. After a piece was made, it underwent a biscuit firing that lasted several days. If it survived, it was glazed and fired a second time. Each color applied to the piece required a separate firing due to differing firing temperatures. Thus, a piece with six colors could be fired up to eight times, making the process highly intricate.
Back in the day, firing a kiln was a significant endeavor, especially with bottle kilns. These firings took days, and the person in charge, known as the fireman, was the highest paid. Using just a shovel and about 15 tons of coal per firing, the fireman had to precisely control the temperature. Over-firing could result in a failed batch, meaning no one involved in making the pottery would be paid. The success of these potteries relied heavily on the skill and teamwork of everyone involved.
Today, firing is much simpler. I have an electric kiln with a controllable panel where I set the temperature and leave it to work while I go about my day. This convenience makes the process far easier.
Pottery decoration has evolved significantly. We can now fire all colours together at the same temperature and apply colours to wet or leather-hard clay and bisque ware. Modern techniques even allow for printing photographs from laser printers to create custom ceramic transfers and complete 3d printed ceramics.
Learn more about Bone China Clay here.